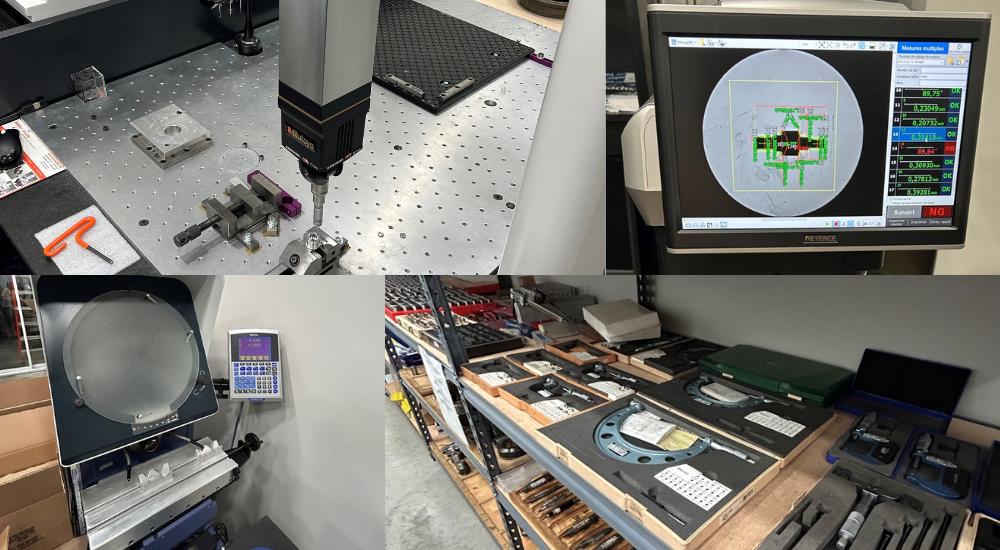
In the world of high-precision machining, even a single inaccurate measurement can compromise an entire production run.
The margin for error is often nonexistent. A non-compliant part—off by even a fraction of a millimeter—can result in a rejected batch, wasted time, and lost credibility.
At APF Villeneuve, we’ve learned that metrological precision begins well before choosing the instrument.
Because we use these tools daily in real production settings, we know how much the selection and maintenance of measuring tools impact the final quality of our parts.
In this article, you'll discover the tools we rely on and the practices that ensure flawless accuracy—even at scale.
Why Every Measurement Impacts Part Compliance
At APF Villeneuve, we manufacture high-precision parts for industries that tolerate no compromise—transportation, manufacturing, energy, and more. Our tolerances often go down to hundredths of a millimeter—or less.
This means every part we produce must be measured, inspected, and validated with extreme rigor at multiple stages of the machining process.
To do this, we use a variety of metrological tools, each selected based on the type of part, geometry to be verified, and required precision.
Whether it’s for a quick in-process check or a full dimensional inspection before delivery, these instruments play a critical role in our quality control process.
Choosing the Right Measuring Tools for Your Production Environment
Among the instruments we use daily, a few have become indispensable:
-
Calipers (manual or digital) are used for quick measurements of length, diameter, or depth. They’re versatile tools we keep close at hand for many operations.
-
Micrometers are essential for finer checks—for example, validating tight tolerances on shafts or bores with high reliability.
-
Bore gauges are used for internal diameters where precision is critical, such as bearing fits.
-
Dial indicators, mounted on magnetic stands, help detect minimal deviations—useful for checking roundness or flatness errors.
-
Coordinate Measuring Machines (CMMs) allow for highly detailed inspections on complex parts, complete with conformity reports.
Each tool serves a purpose. It’s not just about theoretical accuracy—it’s also about user-friendliness, durability, and adaptability to shop-floor conditions.
The Importance of Calibration and Maintenance
A good measuring tool is only useful if it stays true to its function. That’s why APF Villeneuve has implemented strict procedures to ensure regular calibration of all instruments.
For example, our micrometers and calipers are checked at defined intervals using gauge blocks. The CMM is serviced and recalibrated by certified external specialists.
We also train our operators on proper handling and basic maintenance:
-
Never use tools with greasy or dirty hands;
-
Always clean them after use;
-
Store them in dedicated cases to prevent impact damage;
-
Avoid sudden temperature changes that could affect accuracy.
These are simple habits—but essential ones. Precision depends not only on the machine but also on the discipline of the people using it.
Knowing When (Not) to Trust a Tool
We’ve come to understand the limits of each instrument.
A caliper may suffice for some tasks, but when tolerances become critical (±0.01 mm or less), we switch to micrometers or specialized gauges.
This ability to choose the right tool for each context makes a significant difference in final product quality.
Take bearing seats, for instance. The fit is often interference or close sliding fit. A 0.02 mm error can make the part unassemblable.
In such cases, we use a bore gauge paired with a dial indicator—allowing us to get highly precise and repeatable readings, even in series production.
Precision That Builds Trust
Attention to detail doesn’t go unnoticed by contractors.
They know that a part measured accurately, in a shop that values rigor, is a part that will meet specs once installed.
Our everyday use of professional measuring tools reflects this standard.
We don’t just buy instruments—we make them part of our quality culture. Every operator understands the importance of inspection and knows their role is vital to ensuring every part meets expectations.
Manual or Digital? Experience Is Our Guide
We use both manual and digital instruments, depending on the situation.
Digital tools offer fast, unambiguous readings—ideal in a production environment where efficiency matters.
Some models even let us transfer data directly to a computer system, helping with traceability.
That said, manual instruments remain extremely reliable—especially when a tactile read is needed.
In some cases, we prefer direct contact—for instance, validating a press-fit where an operator’s "feel" complements the numeric reading.
Our Philosophy: Quality Is Never an Afterthought
At APF Villeneuve, quality isn’t something we add at the end of the process—it’s embedded in every step. Our measuring tools are proof of that.
They allow us to maintain high precision, produce in-spec parts on the first pass, and deliver a level of confidence our clients can rely on.
We know that contractors want dependable partners who deliver parts without surprises, on time, and within tolerance.
Our commitment to metrology and best practices is a clear sign of that reliability.
Conclusion: Precision Is a Daily Commitment
Quality starts with controlled measurement. A 0.02 mm error is enough to compromise a critical part.
At APF Villeneuve, every micrometer matters—and we prove it daily by delivering parts that are compliant, durable, and perfectly suited to our clients’ expectations.
Trust a team that masters its tools—down to the last micrometer!