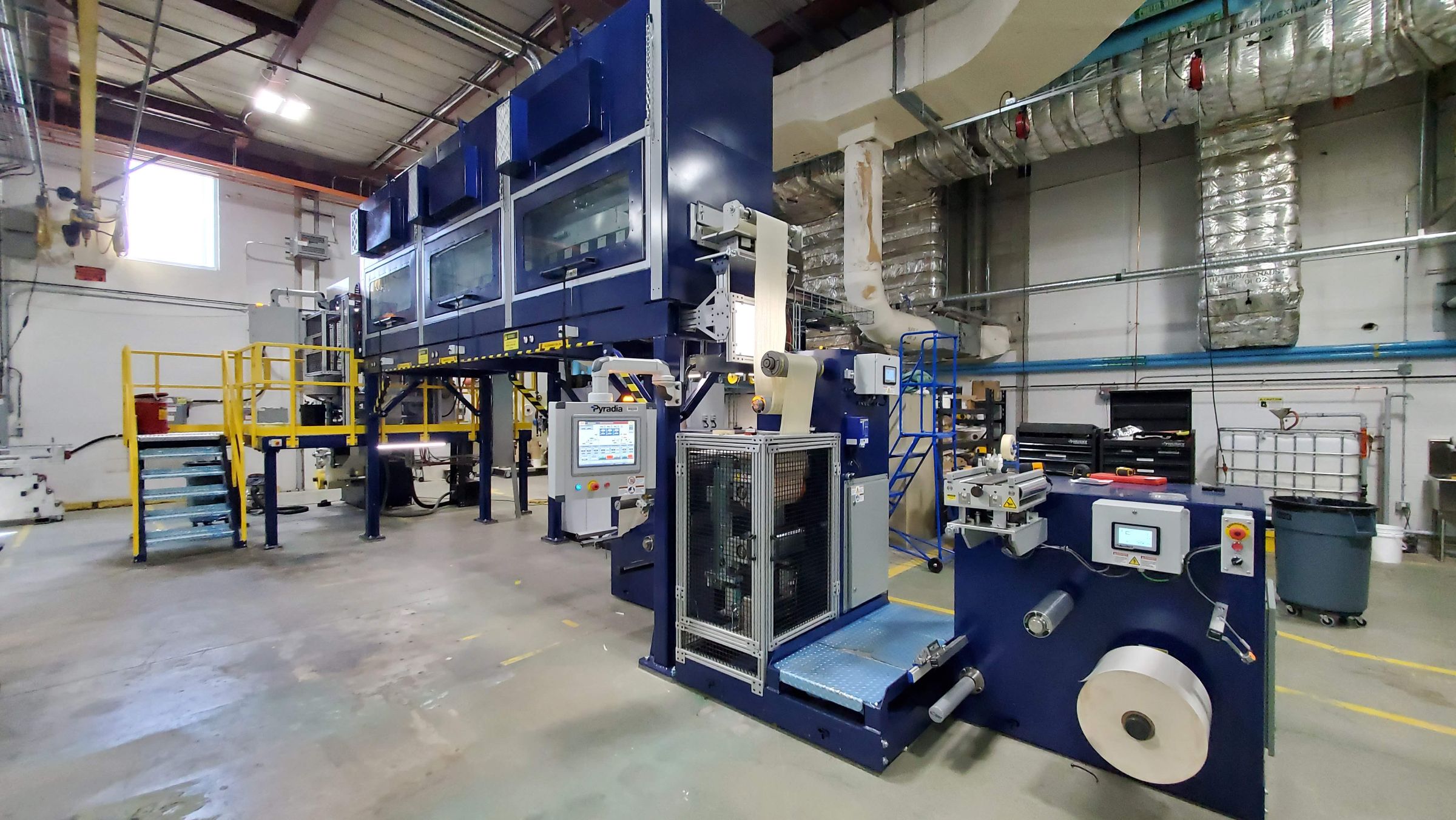
Our customers praise the flexibility and performance of our system, recognizing that it helps to speed up product development, testing and regulatory approvals.
Key advantages:
-
The ability to test several coating combinations and techniques in a single day with quick changeovers;
-
Reduced floor space in R&D and laboratory environments;
-
Optimized system productivity with PLC-integrated zoned safety.
Without access to a pilot line, converters must wait for an opportunity or completely interrupt their production schedules before testing new applications on production machines.
Therefore, Pyradia has solidified its reputation as a leading supplier of pilot coating lines. Our customers can efficiently test smaller-scale equipment without disrupting their production schedules.
A complete, modular solution
A versatile and compact solution is essential in product development, especially when testing new substrates and adhesives. This phase requires a system that can adapt quickly and easily to process parameter changes. Pyradia has developed a modular pilot line enabling rapid changeover among several coating modes within a single coater to maximize flexibility. These modes include direct etching, reverse etching, Mayer rod, comma and saturation, among many others. As such, our customers can test three or four different operating modes daily.
A typical pilot line configuration includes a primary unwinder, a multi-mode cartridge coater, a three-zone flotation dryer, a secondary unwinder, a laminating mill and a winder. This approach offers a complete and adaptable solution to meet our customers’ diverse needs during their many development and testing phases.
Speed and tension control
Pyradia was asked to supply equipment suitable for processing low-strength strip materials. Speed and voltage control are crucially important in any strip converting application. However, pilot lines must operate at extremely low tension when handling delicate substrates such as lightweight, fully saturated non-woven materials. In this context, the tension on a 12-inch strip is kept below a fraction of a pound. This ability to work with minimum tension means that our equipment is particularly well suited to the specific requirements of the delicate materials used in the strip converting process.Haut du formulaire
Optimized, precise safety checks
Pyradia benefits from its partnership with Rockwell Automation to optimize the performance of our pilot coating lines. We use various Integrated Automation Builder (IAB) software features to develop controller-based safety solutions from Allen Bradley®, GuardLogix®, Kinetix® 5700 servo drives and VP series servo motors. The system is integrated into an EtherNet/IP™ network and equipped with an Allen Bradley PanelView™ graphics terminal.
Using servo technology has proven to be an effective method of ensuring precise and flexible belt tension control. Mechanically, the servo motors can be mounted on various rollers as the system switches from one coating mode to another, thanks to their compact casing. Control parameters can be adjusted using the machine interface, offering greater flexibility in the operating process.
Advanced, safe features
Pyradia’s pilot coating lines are equipped with an integrated safety solution, using the advanced Kinetic servo motors and the GuardLogix controller features. With this configuration, the controller and servo motors operate harmoniously on the network, making it possible to create and modify safety zones without rewiring.
The integrated Safe Torque Off function eliminates the rotational power of servo motors without turning off the drive. These capabilities allow operators to adjust specific sections of the machine in complete safety while letting the rest of the process run normally.
All in all, the integrated safety solution provides operators with detailed information. If a guard is opened or an emergency stop is activated, the operator can consult the diagnostics from the interface, enabling them to quickly resolve any problems.